Repairing and replacing docks requires a keen eye to spot the signs of wear and tear. Understanding what issues require repair and when it is time for replacement can save you money and headaches.
Mildew and moss not only compromise the appearance of your dock but may indicate structural damage beneath. If regular cleaning and minor repairs are not helping, consider calling in the experts for a complete evaluation. Click the Dock Repair to learn more.
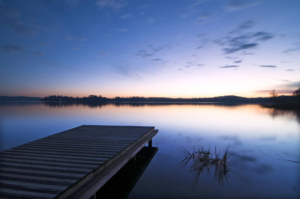
Over time, wood rot and corrosion can damage the structural integrity of docks. A dock that isn’t as solid as it was once is a danger to anyone who walks on it. A dock platform that collapses suddenly can injure people or cause serious property damage. That’s why it’s important to regularly inspect your dock for signs of damage that need attention.
A sign of a serious problem is cracks that appear in the decking. A cracked deck is unsightly and can lead to trip-and-fall accidents. It’s also a risk to any boat that might dock there. It’s also a sign that the structural integrity of the dock has been compromised, so it needs to be repaired or replaced.
Another sign of a serious issue is warping. In metal docks, warping is caused by powerful waves that flex and bend parts of the structure. Wooden docks can also become warped by constant pressure from currents and waves. If a part of your dock is warped and not easily repaired, it’s time to replace it completely.
Other signs of a serious problem include rust in metal components. If you notice rust in several areas of your dock, it’s a good idea to call in professional help right away. A professional assessment will determine whether the rust is only cosmetic and can be repaired, or if your dock’s foundation has been damaged and needs to be replaced.
Another thing to look for is gaps between boards on your dock. While minor gaps are easy to repair, larger gaps between boards can be dangerous and cause slip-and-fall accidents. Having them fixed as soon as possible will prevent potential accidents and increase your dock’s safety. A comprehensive inspection should cover all aspects of your dock, including decking, supports, and auxiliary structures like ladders and cleats. It should also include visual inspections and a test of the stability of your dock at various tide levels.
Wood Rot
Even with the best treatment and care, wood that contacts water will deteriorate and show signs of rot. This is caused by fungi that cause the wood to become soft and spongy. It also often becomes discolored and may smell musty. The good news is that a small amount of rotting can be sanded away, but significant areas of rot must be replaced with new wood to avoid structural damage and safety hazards.
In addition to natural causes of rot, a dock’s foundation can become damaged by marine organisms such as shipworms and other crustaceans. This can happen slowly over time, or in a sudden accident like a boat crash that damages the dock’s pilings. It’s important to have a dock inspector check the dock pilings regularly for this problem and replace any that are showing signs of damage or rot.
The frames of a dock provide both support and stability, so any problems with the frame can have serious consequences for the dock’s safety and structural integrity. These issues can include noticeable bends or cracks, especially in metal frames, as well as rot or decay in wooden ones. Minor problems may be able to be repaired by replacing a few beams or boards, but significant damage can require full replacement of the frame and other parts of the dock.
Another part of the frame that may need to be replaced is the floats. These are crucial for the overall buoyancy of a dock and can become leaking or lose their ability to provide the necessary level of buoyancy over time, especially in rough water conditions. While small leaks in floats can be sealed with sealant, they should be replaced immediately when a serious problem is detected to keep the dock stable and safe for users.
Loose Cleats
The cleats that are used to secure your boat to a dock or wharf provide important safety and security. However, over time they can become loose or even break. This can be due to a number of factors, including overuse or just age. The best way to prevent a loose cleat is to use it only when necessary and to check it regularly for signs of wear. This will help you catch any problems before they get out of hand.
A cleat can be easily fixed with some common tools and materials. First, you’ll need to remove the cleat and clean it of any debris or corrosion that may be present. Then, you’ll need to apply a bedding compound to the base of the cleat. Once you’ve done that, you can replace the cleat and tighten it properly.
Proper cleating skills are vital to any boat owner, as they’re used in high-stress situations like docking and mooring. In fact, many sailors consider cleating to be an essential part of seamanship. Getting these skills down can save you time and money and improve your boat’s performance.
In general, you’ll need a few different types of cleats to keep your boat secure on a dock or pier. Bow lines connect the cleat on your boat’s bow to the cleat on the dock, preventing it from being blown away by wind or current. Stern lines are also important, as they can prevent your boat from drifting away from the dock or wharf.
For each of these cleats, you’ll need to know how to tie a cleat hitch. This simple but effective knot will ensure that your dock line stays securely tied and is easy to untie when it’s needed.
Start by going around the cleat’s base with your dock line. Then, pass it over the first horn on the cleat and under the second horn that you started with. Finally, pull the end of your dock line through this loop and over itself, creating a figure eight shape.
You’ll want to use a cleat that’s made from a sturdy material and has a strong mounting system. For example, you’ll want to choose a stainless steel cleat with a backing plate that can withstand a lot of pressure. You’ll also want a cleat that’s well-bedded in the ground.
Water Leaks
If you’re experiencing water leaks from your dock, the first step is to identify where the water is coming from. This typically means drying the bilge and looking for a source. However, a leaking boat often has many conduits and inaccessible compartments, so the origin point may be hard to determine. A professional can help with this process by inspecting the area and identifying the issue quickly.
A Floating Dock Inspector can help to keep your dock in top condition, providing methods of repair and budget suggestions. These professionals also perform yearly inspections on all components, including pilings and frames – looking out for any signs of damage that can lead to future issues. Investing in preventive dock inspections can save you money on costly repairs later.
Depending on the size and design of your floating dock, disassembly may be required in order to make repairs. The process starts by clearing the work area of any accessories, debris or other objects that can hinder the work. Then, any power sources or utilities should be disconnected from the dock system. After that, the frame sections can be unbolted using the appropriate tools and then either lifted or floated away from the dock.
Before starting the work, it’s essential to wear safety gear such as slip resistant shoes, gloves and goggles. This ensures that you’re protecting yourself from slipping, falling or getting into contact with sharp objects or toxic materials. It’s also important to work in a well-ventilated area especially when using chemical sealants or a plastic welding iron as these tools can produce fumes that are harmful to your health.
Once the work begins, a professional will begin by inspecting the dock posts in the water. This usually involves using scuba or snorkel gear to look at the base of the posts and any nails that may be loose. They will then move onto the wood planks and railings that make up the dock, checking for any rotting or other damages.
If the dock is still under construction, a professional will be sure that all of the hardware is properly compatible and aligned with each other. This will reduce stress on the system, helping it to last longer and be more durable. Then, they will use a deck sealant to cover any holes or cracks in the surface of the dock. This will protect the structure from moisture and insects.